「新世代車両」の驚きの製造システム
インベスターデーでは新車のお披露目こそなかったものの、「次世代車両」では製造コストを半減する革新的な製造方法「アンボックスド(unboxed)プロセス」が紹介されました。これは、1922年にヘンリー・フォードが発案したコンベアラインから発展してきた自動車の製造のフローを抜本的に改変するもので、衝撃を持って迎えられました。
従来の「プレス→車体組立→塗装→最終組立」という4段階の自動車製造プロセスは、プレス加工した鋼板をボディシェル(ホワイトボディ)に組み上げてからシェルの状態で塗装します。最終組立工程では、最初にドアを外してからカーペットやシート、内装部品を作業員が組み付け、最後にエンジンやサスペンションを組み込んだ車台を下からドッキングさせるという手順です。
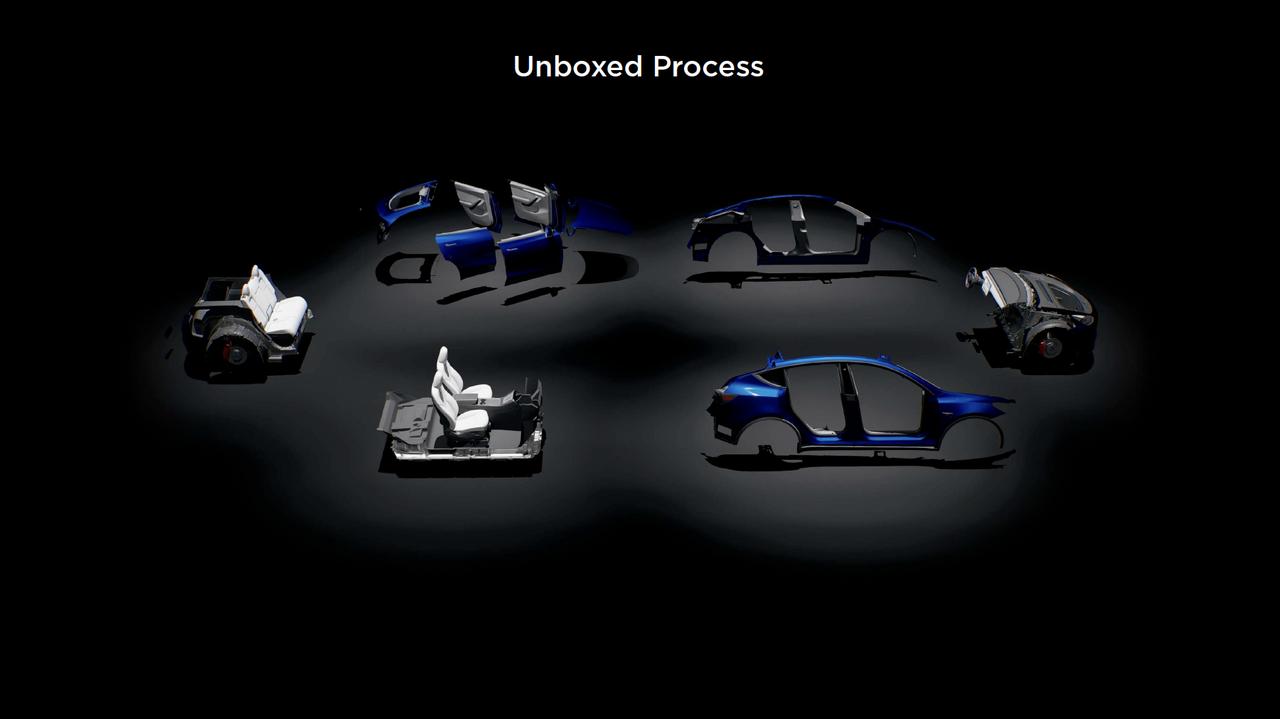
まるでプラモデルを組み立てるように見える「アンボックスド(脱箱型)生産方式」。塗装工場を筆頭に工場面積は大幅に縮小できそう。
テスラは、これを車両前部、後部、左右のサイドアッシー、ドアアセンプリー、フロアの6つの群に分けてそれぞれ組み付けた後、最後に一気に合体させる方式を採用すると発表しました。これによって、各群で同時進行する作業が飛躍的に増え、作業密度で44%、時空効率で30%削減できるとしています。工場の敷地面積(footprint)は4割削減され、投資額も抑えられることで車両コストを5割削減できるというわけです。
ギガプレスをフロントセクションにも。電池パックを構造体に
すでに、上海工場生産の「モデルY」では、リアフロアセクションを一括で鋳造する「メガキャスティング」を採用して、何百ものプレス部品とその溶接を不要にしていますが、これをフロントセクションにも導入。塗装は、必要なドアやボンネットなどの外板パネルのみ行うことで、長い塗装ラインも不要になります。
また電池パックをボディの構造体とすることで、衝突安全性やボディ剛性も担保するという考え方は「モデルY」から導入されており、電池パックを土台とするフロアにカーペットやシート、コンソールなどの内装部品を載せた上で、アッセンブリーするという工程になります。

重く嵩張るシートのキャビン内への組み付けは重労働の最たるものだったが、この方式ならロボットにもできるかもしれない。
eドライブユニットは一機1000ドル以下にコストダウン
eドライブユニットでは、モーターはレアアースの使用をゼロとし、パワーエレクトロニクスのマイクロプロセッサーを自社設計してシリコンカーバイトの使用量を75%削減。次世代の内製eドライブユニットのコストを一機1000ドル以下で製造することを可能としたようです。
さらに、サイバートラックからは過去60年間12Vが標準だった自動車の電装システムを48V電圧に変更し、車内のキャンバス通信を全てイーサネットに切り替えて高速化と省電力化を図り、次世代車両ではコントローラーを100%自社設計するなど、その技術革新には目を見張るものがあります。
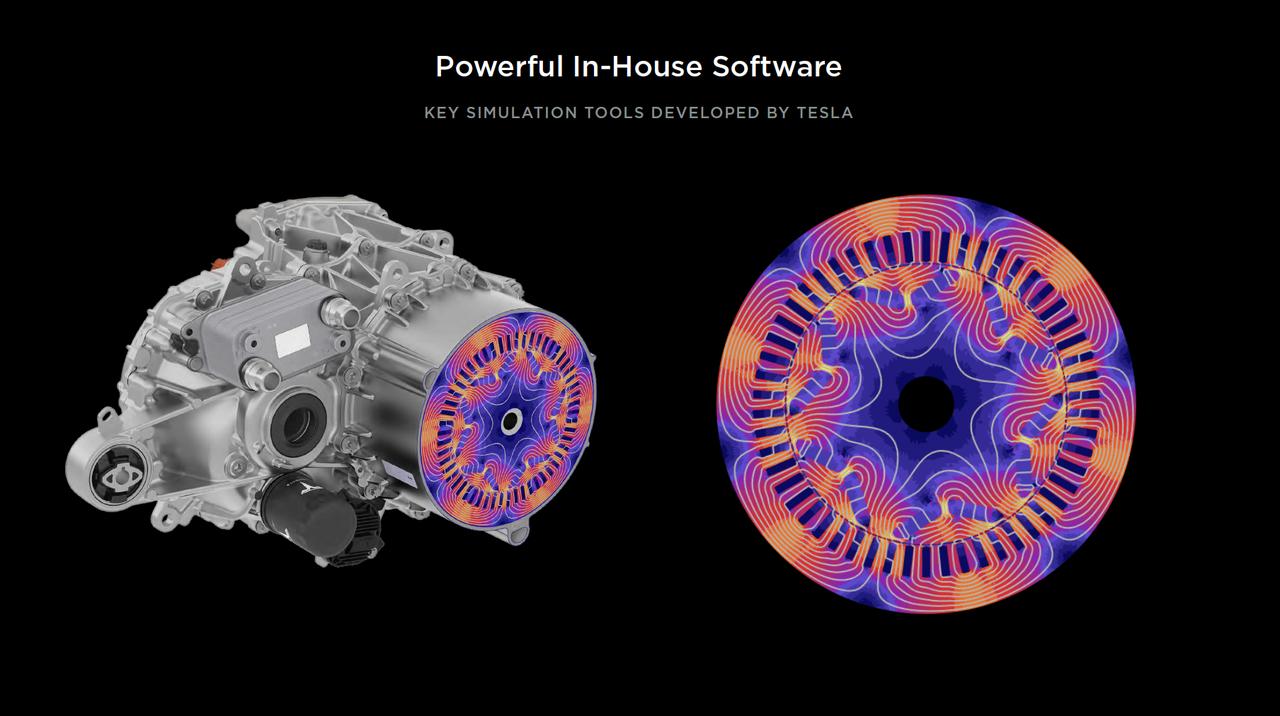
モーターの磁界のシミュレーションも自社製ソフトで最適化。
このようにして、「次世代車両」ではコストが半減するとしており、米国境の南200kmのメキシコのモンテレイ(Monterrey)に建設されるギガファクトリーで生産されるモデル(「モデル2」と予想)は2万5000ドルを実現することになるのでしょう。上海工場を9ヶ月半で完成させた実績から考えると、2024年内にも新世代車両第一号がラインオフしそうな気配です。
マスクCEOは、2つの新世代モデルで合計500万台は生産するだろうと述べました。下の図でヴェールのかかった右端の一台は「モデル2」として、その左横はSUVかバンのように見えます。一方、株主総会でシルエットが写された車は「モデルY」のような形状で「ロボタクシー」を思わせました。果たして2車種目は何なのでしょうか。
ちなみにマスクCEOは、会場の質問に対して、2000万台作った時点でも総モデル数はせいぜい10車種くらいだろうと回答しています。さらに「テスラロードスター」の新型モデルもデザインは固まっており、上手くいけば2024年中に生産を開始できるかもしれないとのことです。
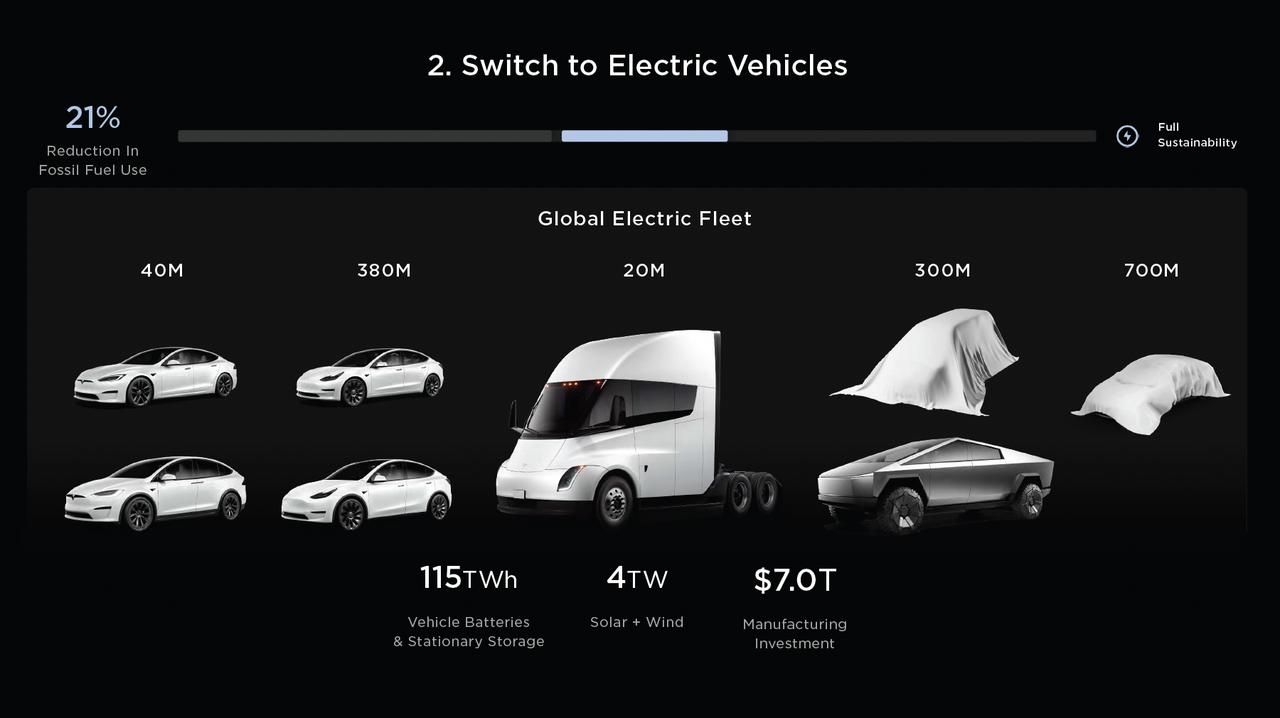
インベスターデーで紹介されたEVラインアップ。中央はネバダ工場で生産が始まった「セミ(Semi)」トラック。