バッテリーも“手の内化”。アルミ鋳造一体化技術も採用
ホンダは2020年代後半にEVは本格的な普及期に突入すると予想している。そのため注力しているのがさまざまな「生産構造の改革」だ。
まずはバッテリー生産の“手の内化”である。EVはその生産コストの3〜4割をバッテリーが占めるが、その調達コストを抑制かつ競争力を高めるため、パートナーとの協業比率を高めて “手の内”化を進めていく。2025年にはLGエナジーソリューションとの合弁によって設立された新工場で年間40GWhのバッテリー生産が始まる。また、先日発表されたとおり、2020年代後半にはGSユアサと共同開発した自前のバッテリー生産もカナダの新工場で始まり完全な垂直統合型のバッテリーサプライチェーンが完成する。2030年には、北米で調達するバッテリーコストを現在より20%削減する。
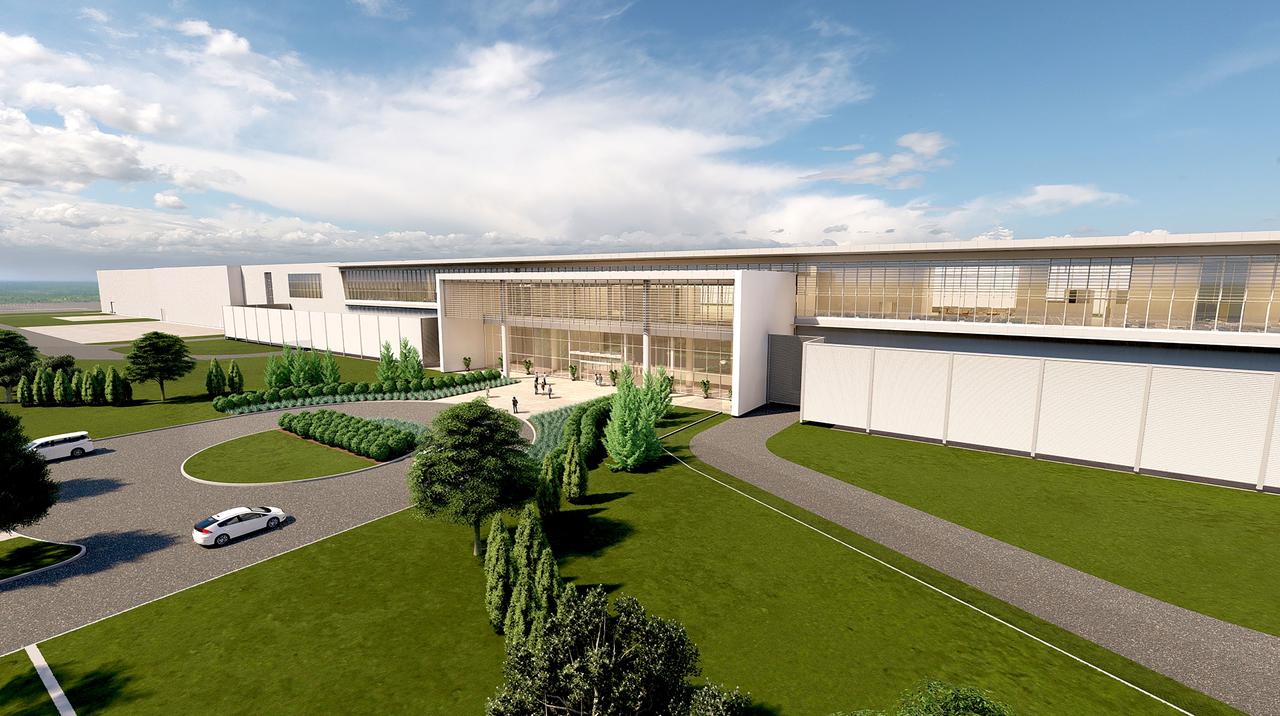
2025年から稼働を開始するLGエナジーソリューションとの合弁工場(イメージ)。ここで生産されるバッテリーは「SALOON」から搭載が始まる。
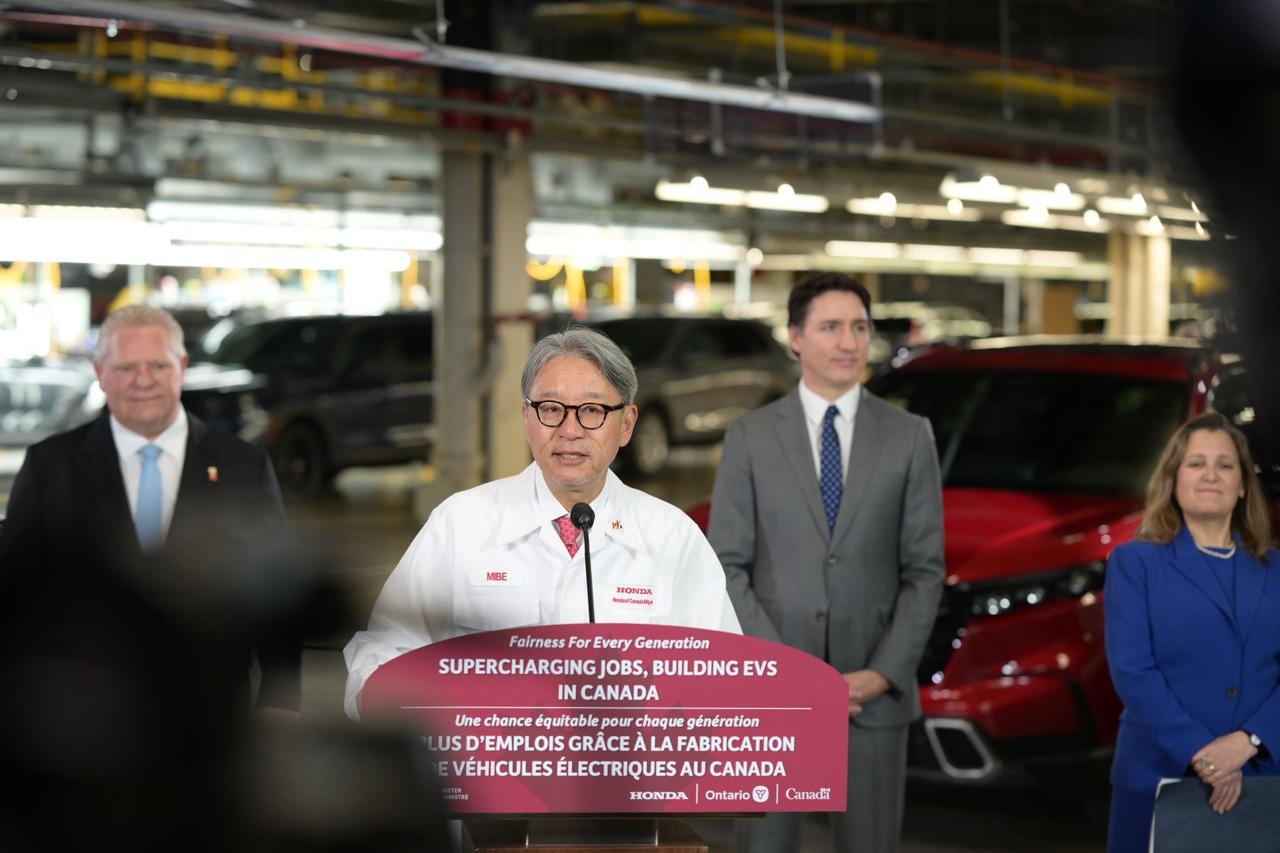
カナダに新設されるEV専用工場では、バッテリー生産から車体最終組み立て工程まで垂直統合。年産25万台の生産キャパシティで2028年から稼働する。
生産方法にも大きな変革が訪れる。2026年のZEROシリーズ立ち上げとともに、米オハイオ工場の車体組立・溶接ラインも一新されて「ICE・EV」の混流生産ラインが立ち上がる。溶接には世界初の「CDC接合技術(複数の異なる板厚の素材を溶接する技術)」が適用され、既存工場のラインを大きく変更することなく、車体生産工程を大幅に簡略化。カナダのオンタリオ州に新設されるEV専用工場ではさらなる高効率化を追求して、生産コストを35%も低減したEV生産を計画している。
そしてホンダもついに「メガキャスト」を導入する。と言っても、いきなりアンダーボディを一体成型するわけではない。まずはバッテリーケースの一体鋳造から始め、ZEROシリーズの薄く軽い車体の実現にひと役買う。「メガキャストやギガキャストですべてが解決するわけではない。ボディの修理などで課題は残っている。まずは大物アルミ部品であるバッテリーパックを薄く高精度で仕上げる(三部社長)」。
なお、このバッテリーケースと関連部品の接合には3D摩擦撹拌接合(FSW)が用いられる。この生産方法はまずはオハイオ工場に導入され、ボディ骨格には2028年以降をめどに稼働を開始するカナダのオンタリオ工場で生産されるEVでの採用を検討しているようだ。