「アンボクストプロセス」をモデル2で初採用
年初の決算発表では、「レッドウッド(Redwood)」と呼ぶ低価格EVの開発プロジェクトの存在を正式に表明した。通称「モデル2」と呼ばれてきたその新型車は、SUVタイプのコンパクトなEVであり、テスラの弱点と言われる大衆車セグメントで価格競争力のあるEVだという。2025年後半の発売を計画しているようだ。
では高い価格競争力をどのようにして実現するのだろう。マスクCEOは「画期的な生産プロセスを実現して世界を驚かせる。2024年はそれが実現するまでの狭間にある」とコメントした。つまり、“今年はたいしたことやらないけど、2025年には凄いことやるから期待していて!”とアピールしたかったのだろうが、肝心の“凄いこと”に関しては具体的な情報の開示はなかった。
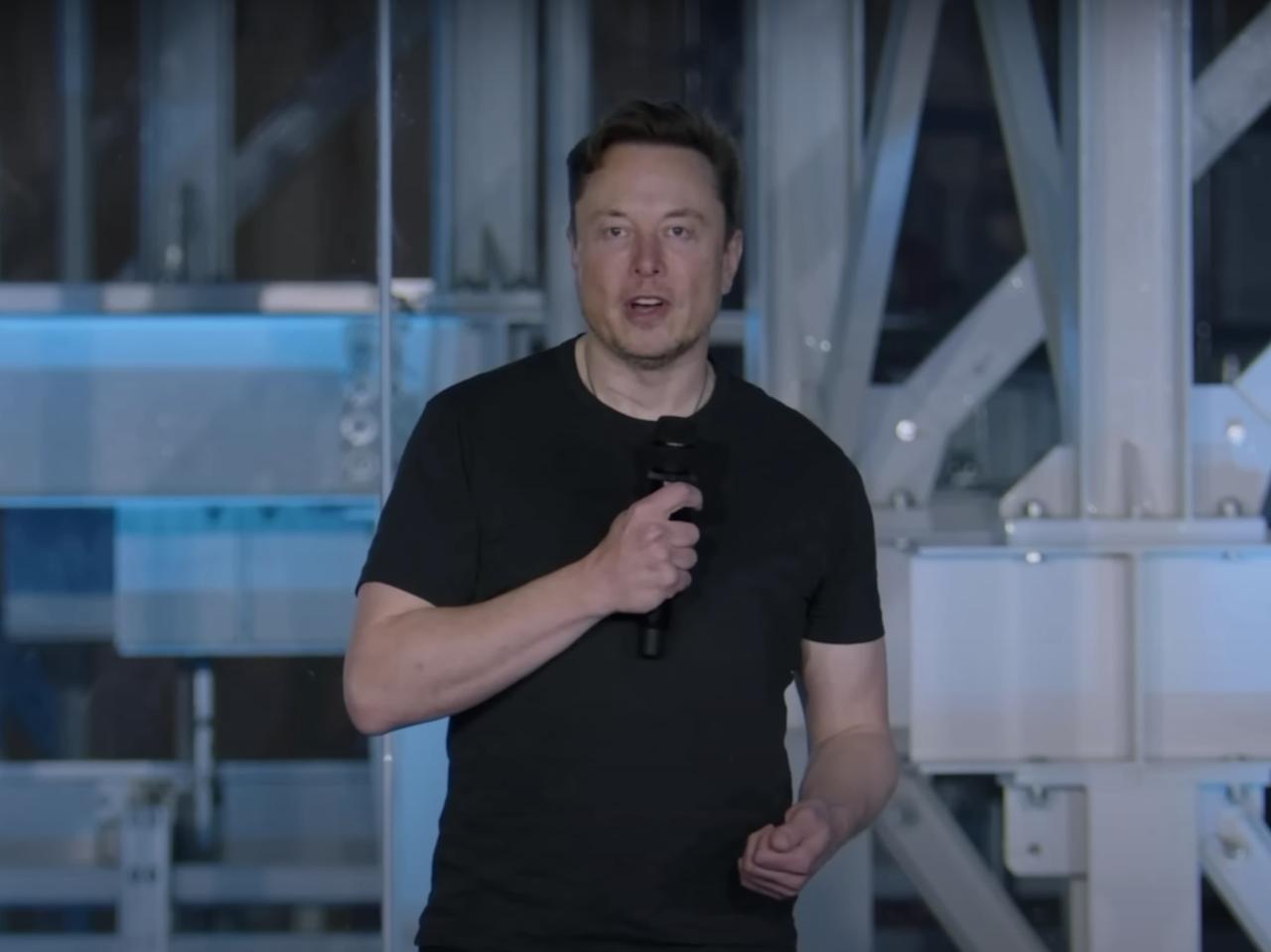
2025年には次の成長フェイズに入るとアピールするイーロン・マスクCEO。(2023年3月に開催された「Tesla’s 2023 Investor Day」にて)
では、「画期的な生産プロセス」とは何なのだろう。実は2023年5月に開催されたイベントで、すでにその概要は説明されていた。「アンボクストプロセス(Unboxed Process)」と呼ばれる生産方式だ。それは100年以上も連綿と続いてきた自動車の生産プロセスとの決別である。自動車の生産にかかる時間を大幅に短縮し、生産に必要な工場スペースも縮小する。つまるところ、クルマの価格も下がるのだ。
完全モジュラー生産による工程の並列化
1900年代前半にヘンリー・フォードが生み出したベルトコンベアによる生産ライン方式は、いまも世界中の自動車メーカーが採用する(テスラも例外ではない)。ボディ、つまり“箱”を先に組み立ててからラインに乗せ、その中に人が乗り込んで順番に部品を組み込んでいく生産方式だ。パワートレーンやサスペンション、複雑で重く長い配線や内装部品などを順番に取り付けていく。最後にドアパネルやボンネットフードなどの外装部品を取り付けてようやく一台のクルマが完成する。これでは生産時間の短縮に限界がある。しかも長大なラインスペースが必要なので、工場の規模も大きくならざるをえない。
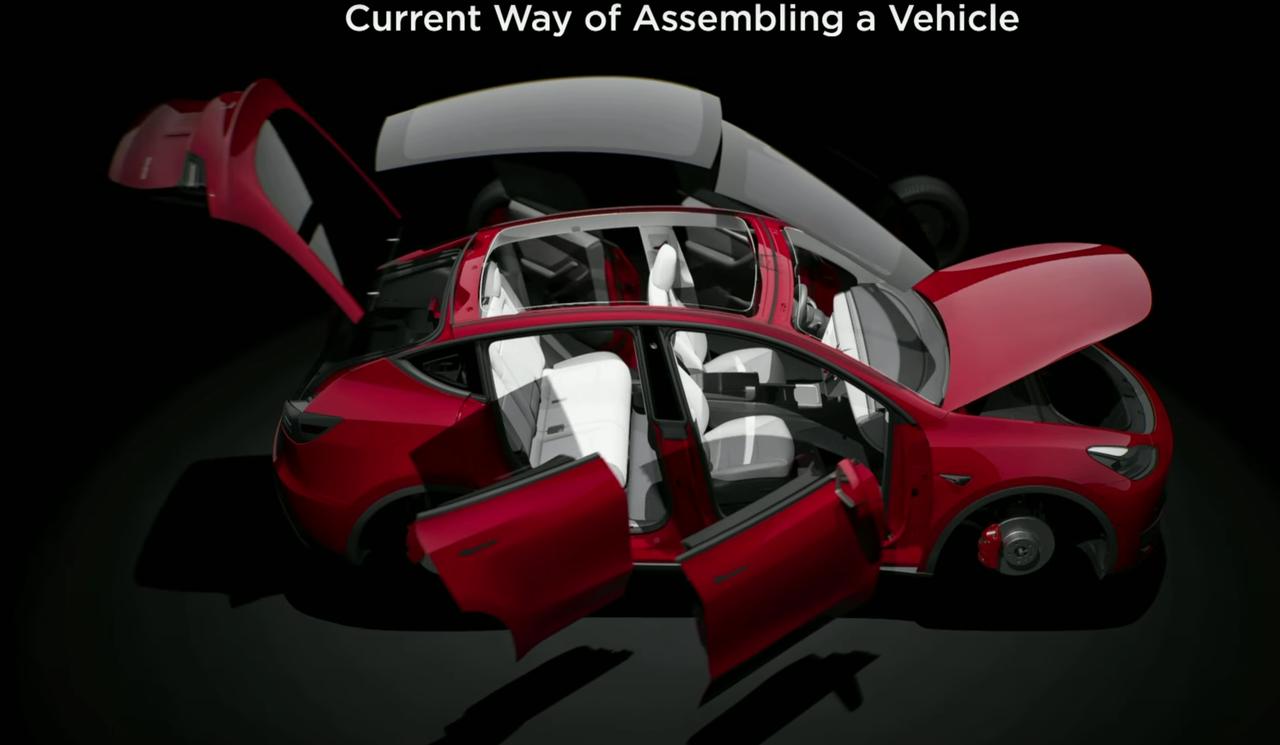
従来の生産プロセスでは組みあがったボディをラインに乗せて順番に部品を組み込んでいく。1台当たりの生産時間の短縮には限界がある。
対してアンボクストプロセスでは、アンダーボディを3つの基本モジュールに分け、それぞれ並行して部品を組み込んでいく。モーターを始めとするパワートレーン関係一式、足まわり、そしてシートやコンソール、インストパネル等などがそれぞれのモジュールごとに並行して組み込まれていくから長大なラインは不要だ。最後に別工程で制作された塗装済みのパネル類(左右に分割されたボディパネル、ボンネットフード、ドアほか)を装着し、ようやく“クルマ”になる。
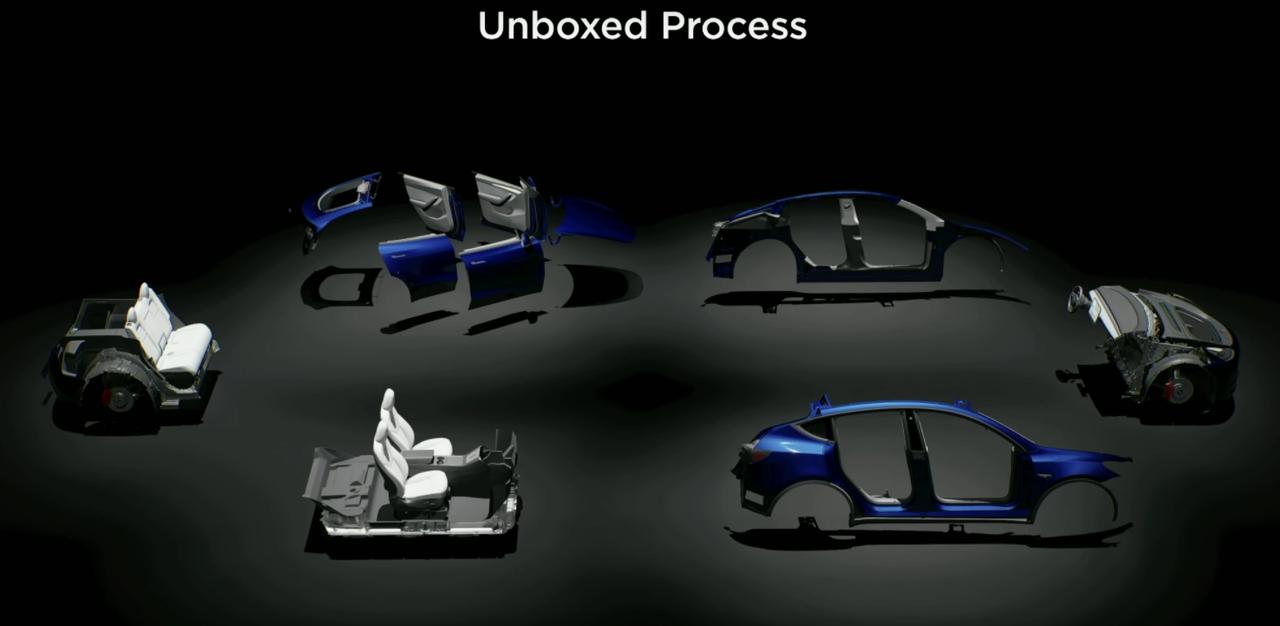
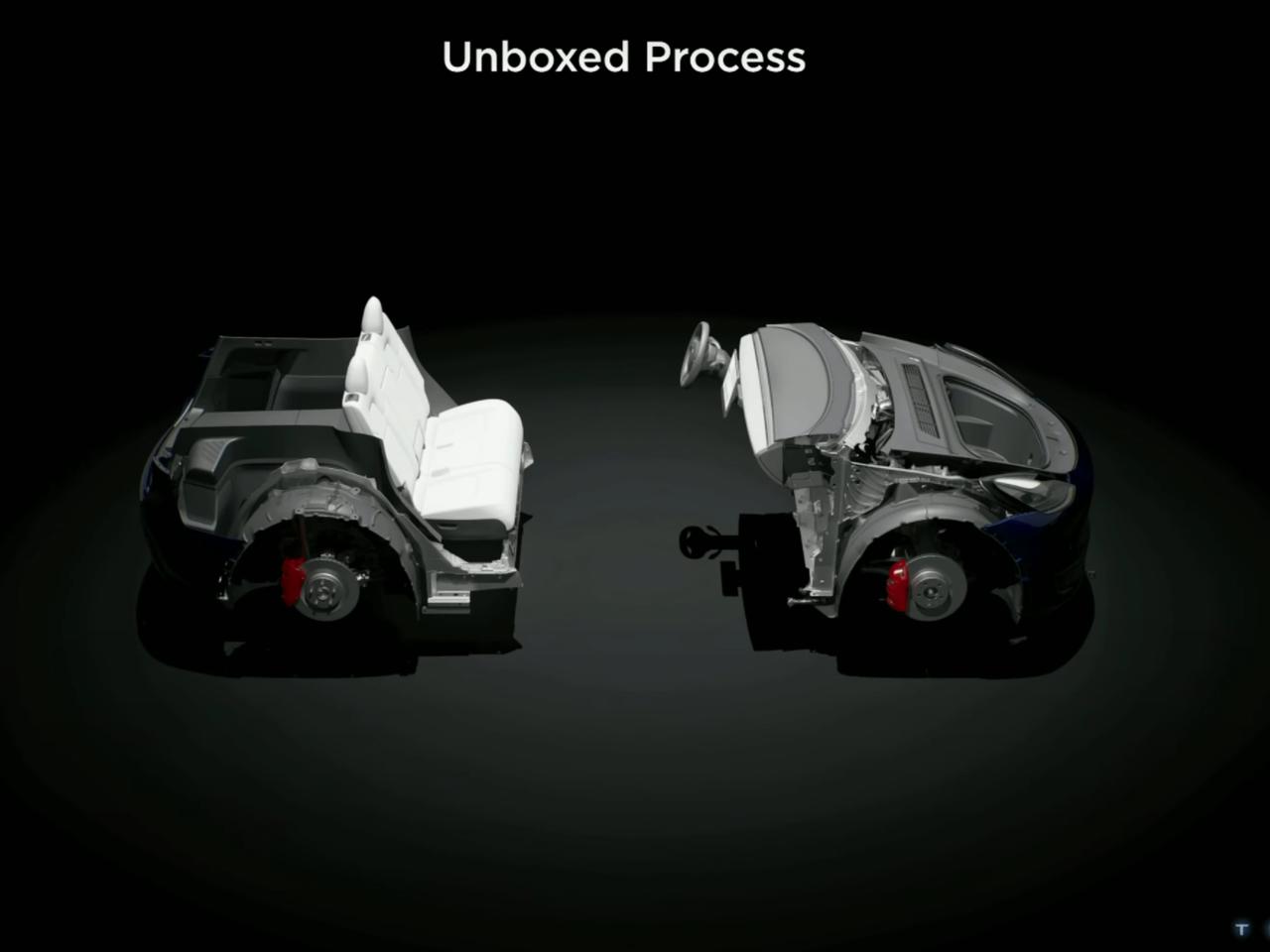
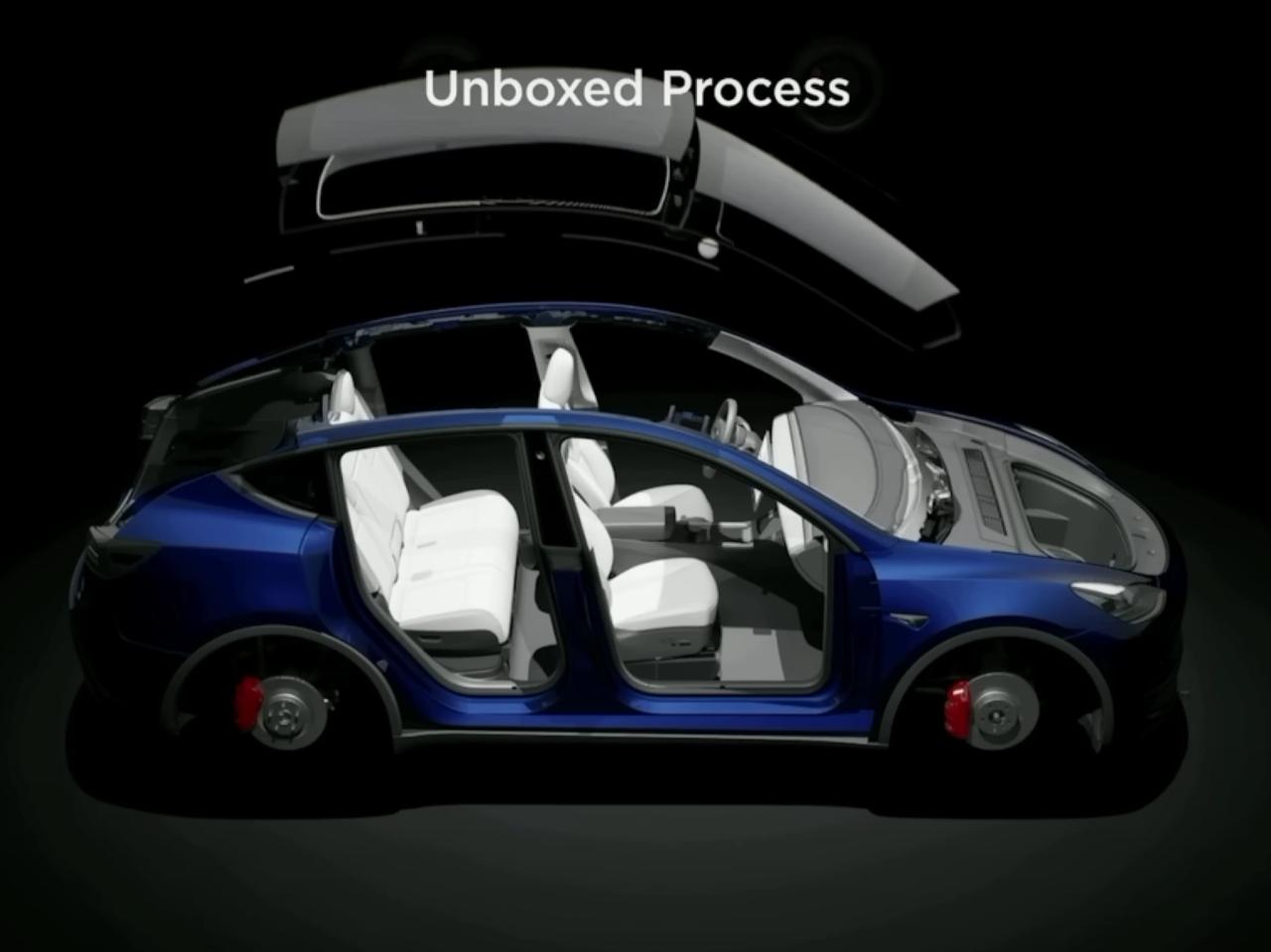
3つの基本モジュールや外装パーツを別々にほぼ完成に近い状態に仕上げたのちに一体化して組み上げる。
生産工程が並列化されることにより長大なラインは不要となり、作業員がクルマの中に乗り込んでアセンブルする工数も大幅に減る。ゆえに“unboxed process”と呼ぶわけだ。工数を40%削減し、コストも50%下げることができるという。つまり、安価なEVをまるでプラモデルを作るように短時間で大量生産することが可能になる。
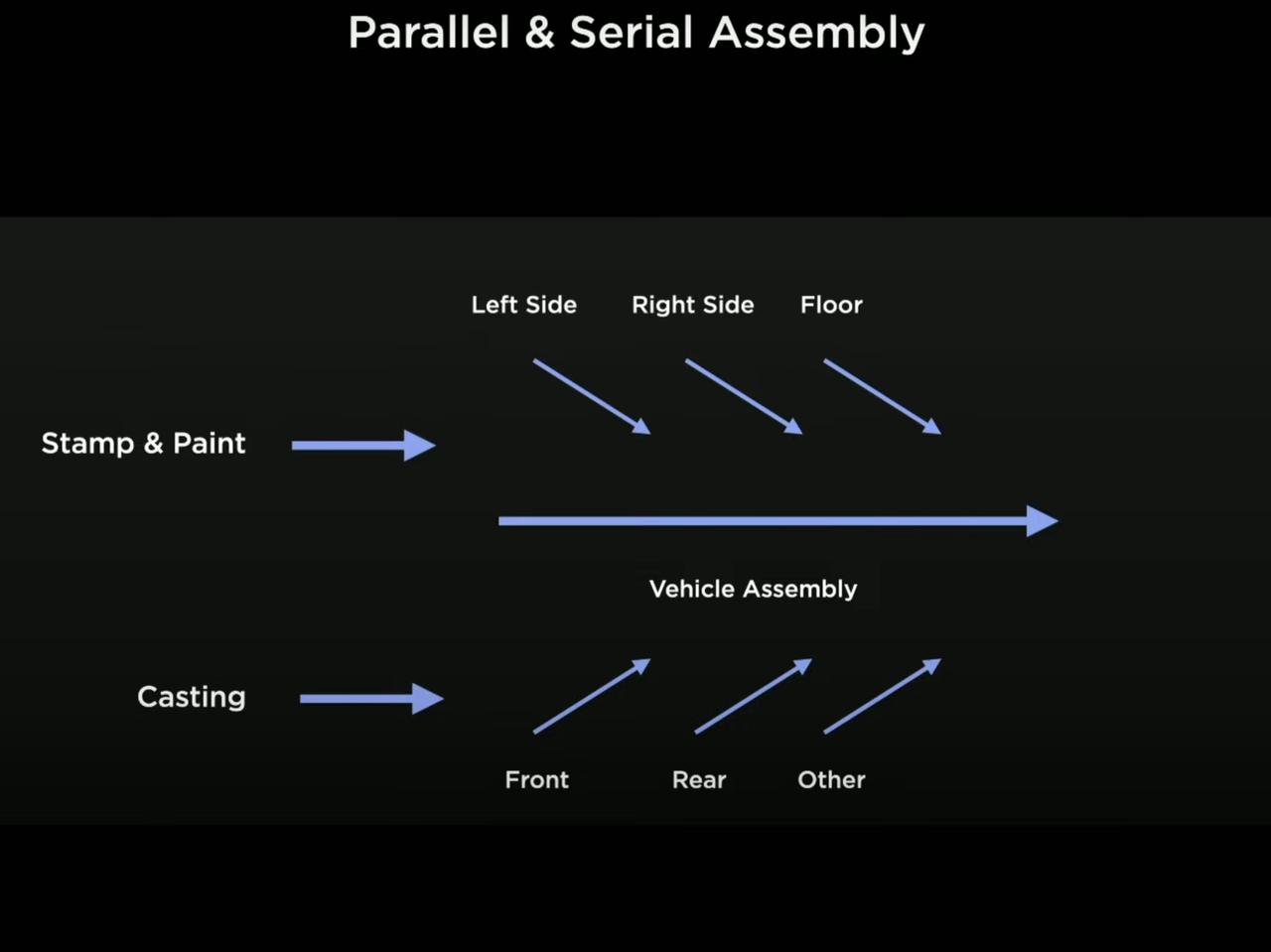
モジュール単位で組み立て作業を並行して行うことで生産効率は劇的に向上する。