コストを大幅削減する手段として注目
ギガキャストの採用は米テスラがその先陣を切ったが、中国メーカーも追従、トヨタを始め、米GM、欧州勢もボルボやフォルクスワーゲンなども採用を表明している最先端の製造技術だ。
従来の自動車では、板金プレス加工した数十点のパーツを複雑な溶接工程を経て大型の構造部品を生産していた。ギガキャストでは、大型の金型に溶かしたアルミ合金(「溶湯」と呼ぶ)をふたつの型(固定型と可動型)のあいだに高速かつ高圧をかけて流し込み一体成型する。
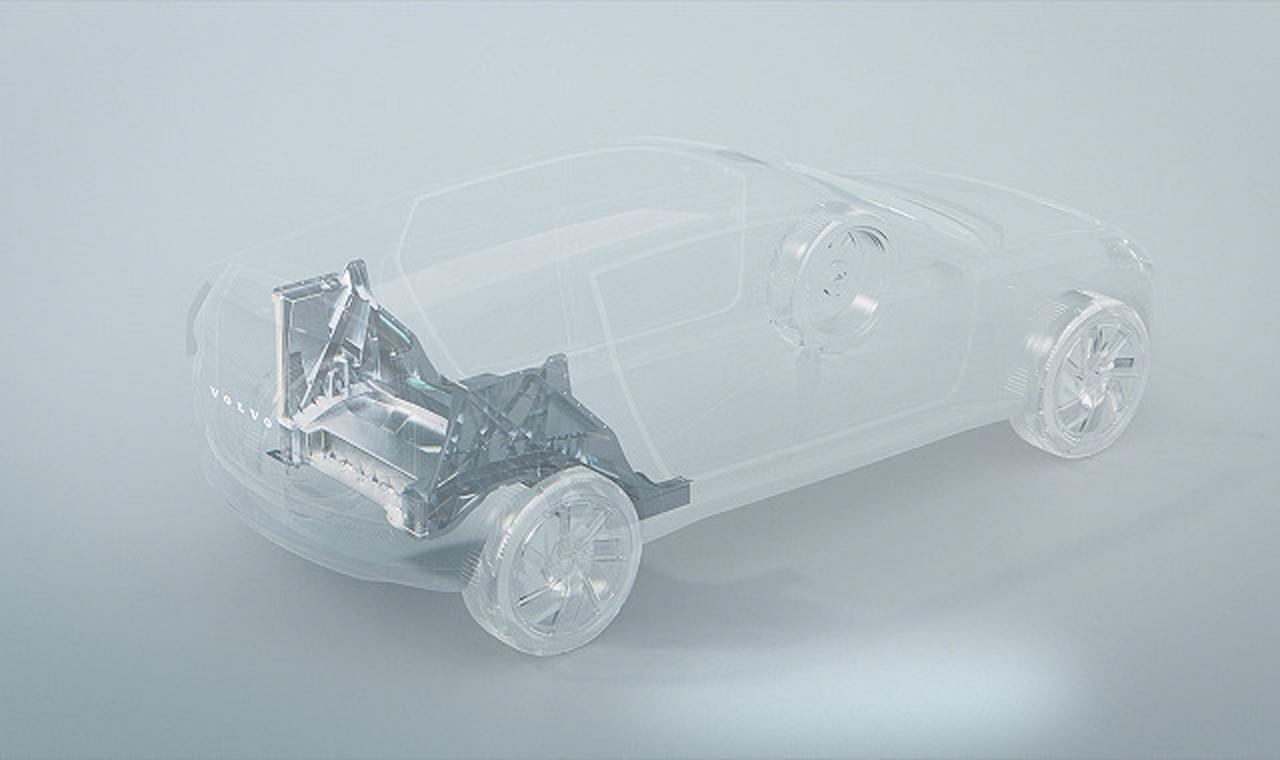
ボルボも次世代EVの構造部品にギガキャストを採用する。
従来工法で必要だった膨大な工程が、ワンプレスで済んでしまうのだ。その結果、長大な溶接ラインが不要となり、高価なアルミ合金を使っても、コストは大幅に圧縮できる。
「鋳物」というと型から取り出された状態では粗が多く、あとから職人がヤスリをかけて仕上げる様をイメージする方もいるかもしれない。しかし、現代の技術では、むしろスチールの溶接よりも精密で正確な寸法出しが可能になっている。強度も均質で、設計値に忠実だ。仕上がり面は美しく、あとから加工したりする必要もない。
自動車メーカーの課題をギガキャストが解決する
良いことづくめと思われるが、課題がないわけではない。一体成形となれば、当然出来上がった部品が大きくなるので、それをストックしたり組み立て工場に運んだりするサプライチェーンの抜本的な改革が必要になる。
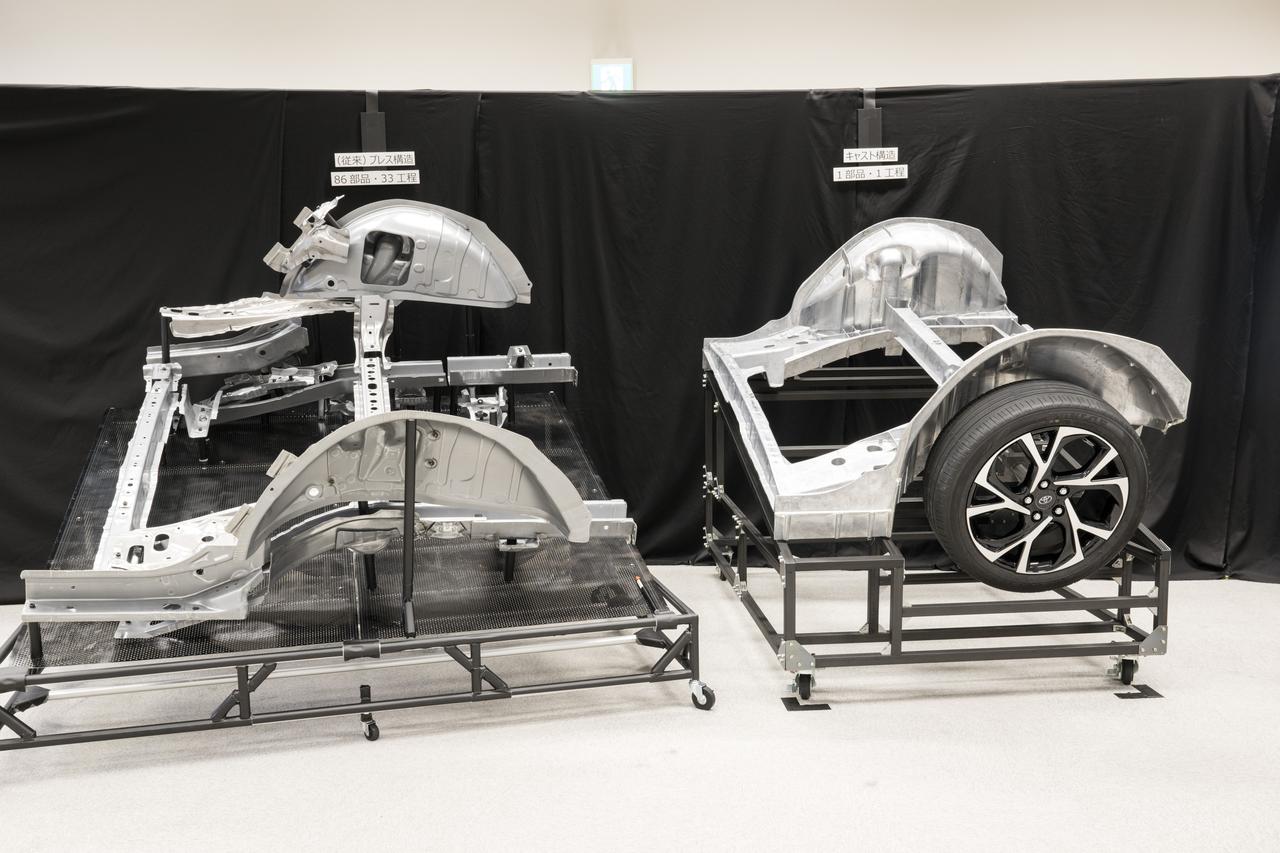
トヨタが公開したギガキャストの例。左は従来の溶接工法。86点もの部品と33工程を経てようやく完成させる。対して右のギガキャストは部品1点で工程もひとつに集約される。
トヨタはその問題を自社工場内にダイカストマシンを設置することで解決するようだが、ダイカストマシンは小さなビル1棟分と揶揄されるほど巨大である。生産ラインそのものは短縮されるものの、どのメーカーの工場でも設置できるというわけではない。そのため、国内メーカーはその利点を認めつつも導入には及び腰だった。
そこに手を挙げたのがリョービ。同社は長年、エンジン、トランスミッションケース、シャシ関連など大型アルミ鋳造部品を幅広く手掛け、国内を始め海外の自動車メーカーに供給してきた実績がある。
今回発表された計画では、同社の菊川工場(静岡県)敷地内にギガキャスト用工場建屋を新設、日本初の6000トンクラスのダイカストマシンを導入して2025年3月を目途に稼働を開始するとのこと。ちなみに「6000トン」とはプレス圧力のことである。
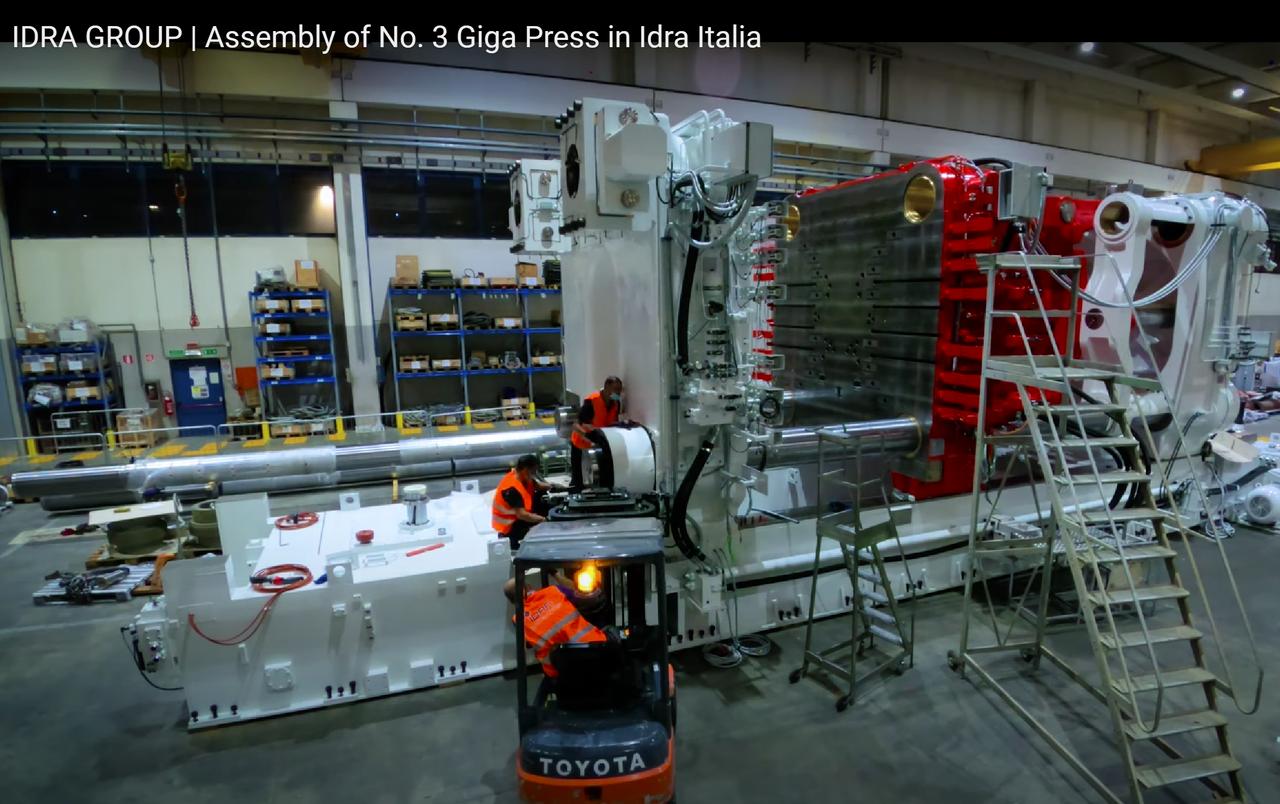
伊・イドラ社の公式YouTubeチャンネルより。ダイカストマシンのスケール感はこの動画を見るとよくわかる。
次世代車に採用が進むことは間違いなし
まずはギガキャストの採用を検討している自動車メーカーに向けて、新型車用大型構造部品の試作品製作から始める。菊川工場は地理的にトヨタやスズキの工場と近く、完成部品の輸送問題は最小限に抑えられるだろう。リョービは静岡県の菊川工場のほか、本社のある広島県に2拠点、静岡県にもう1拠点の生産工場をもつ。
ちなみにダイカストマシン本体を受注・製造する企業は、テスラが採用した伊・イドラ(アイドラ)社を始め、ボルボが採用を表明しているスイス・ビューラー社、中国LKグループなど。日本ではUBEマシナリー、芝浦機械が知られている。
いずれもプラントのように、プレス圧力や工場の環境などに合せて1台ずつ設計されたカスタムメイドだ。ちなみにイドラ社はテスラからプレス圧力8000トン級マシンの受注を獲得したことも表明しており、これはテスラが開発中の「サイバートラック」に採用されると言われている。
リョービの参入によって、今後発売される次世代車にはメーカーを問わずギガキャストが積極的に採用されるようになるのは間違いない。敷地の限られた国内自社工場にギガプレスマシンを導入しなくても、大型一体成形部品を調達できる道筋ができたのだから。近い将来、ボディ外板は樹脂で中身はオールアルミ一体成形のクルマが登場するかもしれない。